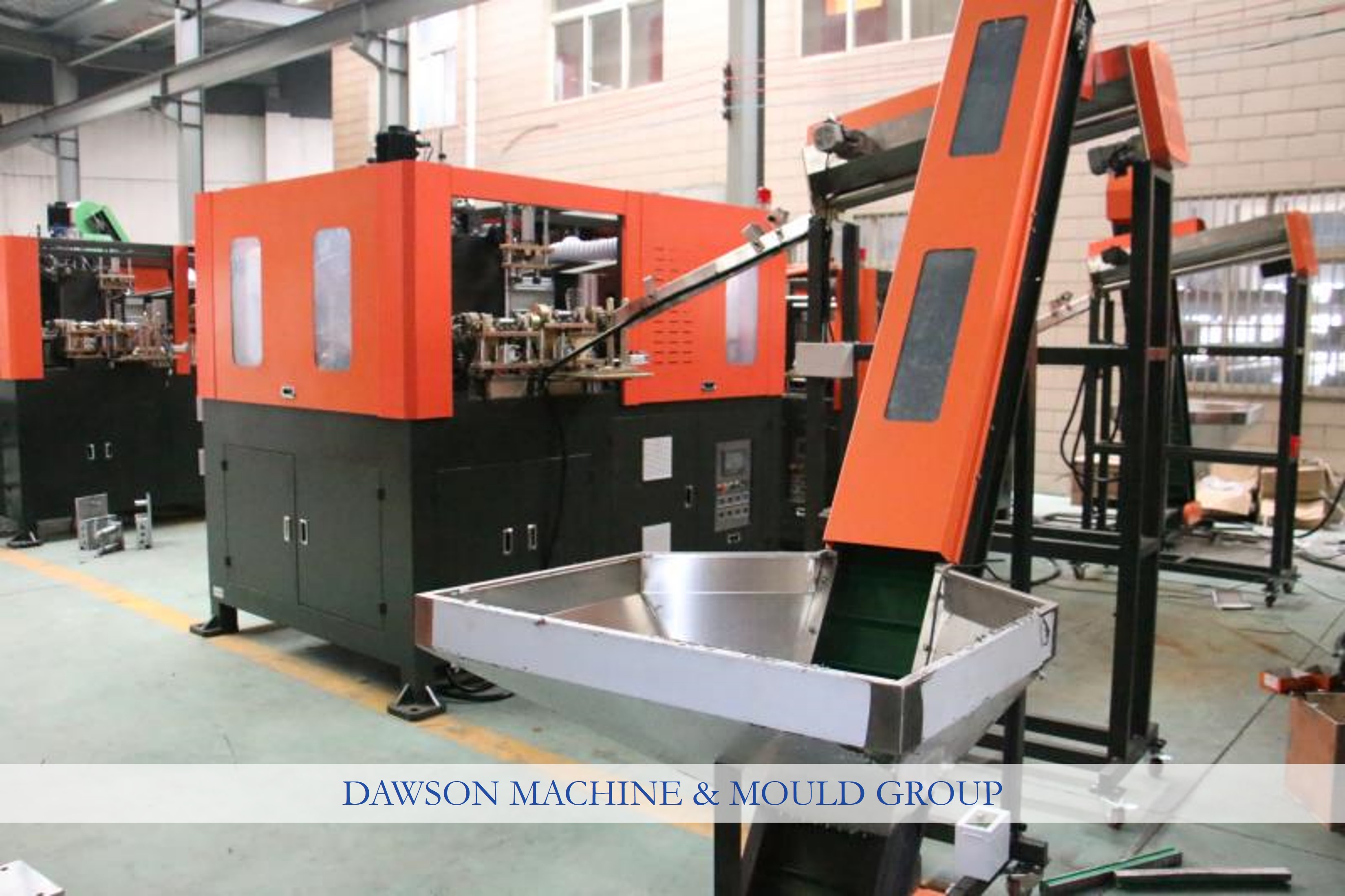
In the dynamic and ever - evolving landscape of plastic packaging, PET (polyethylene terephthalate) blow molding technology has emerged as a shining beacon of innovation. As consumers around the globe become increasingly conscious of environmental issues and demand both sustainable packaging solutions and high - quality products, the advancements in PET blow molding machines are playing a pivotal role in steering the production of plastic bottles towards uncharted territories of efficiency, sustainability, and design versatility.
Efficiency Boost through Technological Upgrades
The latest generation of PET blow molding machines represents a quantum leap in terms of technological sophistication. These state - of - the - art machines are equipped with advanced automation control systems that operate with a high degree of precision. For instance, they can precisely regulate the temperature, pressure, and flow rate of the molten PET material during the blow - molding process. This level of control ensures that each plastic bottle produced is of consistent quality, with minimal variations in wall thickness and overall dimensions.
Intelligent processes have also been integrated into these machines. Through the use of sensors and real - time monitoring systems, the machines can detect any potential issues or anomalies during production. If, for example, the pressure in the mold is not within the optimal range, the machine can automatically adjust it to prevent the production of defective bottles. This not only reduces waste but also significantly improves the overall efficiency of the production line. By minimizing downtime for adjustments and rework, manufacturers can increase their production output, ultimately cutting costs and enhancing their competitiveness in the market.
Moreover, the automation capabilities of these machines extend to the material handling and bottle - ejection processes. Robotic arms can be programmed to pick up the finished bottles from the mold and place them onto conveyor belts for further processing or packaging. This not only speeds up the production process but also reduces the risk of human error and contamination.
Lightweight Design and Diversified Bottle Shapes
Modern PET blow molding machines have embraced the trend of diversification in bottle shapes and lightweight design. Through meticulous optimization of mold designs, manufacturers can now create plastic bottles in a wide variety of shapes, from traditional cylindrical designs to more complex and ergonomic forms. For example, some beverage companies are opting for bottles with unique contours that are easier to grip, especially for on - the - go consumption.
The focus on lightweight design is also driven by multiple factors. Firstly, it reduces the amount of PET material required for each bottle, which in turn cuts down on raw material costs. Secondly, lighter bottles are more energy - efficient to transport, as they require less fuel to move from the manufacturing facility to the distribution centers and ultimately to the retailers. This has a positive impact on the overall carbon footprint of the product's supply chain.
To achieve lightweight yet durable bottles, manufacturers are using advanced materials and production techniques. For instance, some PET blow molding machines are capable of producing bottles with a multi - layer structure. The inner layer can be designed to have excellent barrier properties to prevent the leakage of liquids or the permeation of gases, while the outer layer can be made more rigid to provide structural integrity. This combination of properties results in a bottle that is both lightweight and strong enough to withstand the rigors of handling and transportation.
Environmental Awareness and Circular Economy
In the context of the global push for sustainable development, both manufacturers and users of PET blow molding machines are increasingly cognizant of the need for eco - friendliness. One of the most significant trends in this regard is the adoption of circular economy models. Many companies are now committed to recycling discarded PET plastics and using them as raw materials for producing new plastic bottles.
Some PET blow molding machine manufacturers have developed specialized equipment that can process recycled PET materials effectively. These machines are designed to handle the unique characteristics of recycled PET, such as its varying levels of purity and viscosity. By incorporating recycled PET into the production process, companies can significantly reduce their reliance on virgin materials, thereby minimizing the environmental impact of plastic waste.
Moreover, the use of recycled PET in bottle production also aligns with consumer preferences. Today's consumers are more likely to support brands that are committed to environmental sustainability. By using recycled materials in their packaging, companies can enhance their brand image and attract environmentally - conscious consumers.
Global Market and Competitive Landscape
The global PET blow molding machine market is a highly competitive arena. Manufacturers from different parts of the world, including China, Europe, the United States, and emerging markets, are constantly vying for a larger share of the market. In China, for example, there has been a rapid growth in the manufacturing of PET blow molding machines. Chinese manufacturers are known for their ability to produce high - quality machines at competitive prices, often leveraging their large - scale production capabilities and cost - effective labor.
European manufacturers, on the other hand, are renowned for their technological innovation and precision engineering. They are at the forefront of developing advanced features such as energy - efficient heating systems and highly automated production lines. American manufacturers are also making significant contributions to the industry, with a focus on research and development to create machines that meet the specific needs of the North American market.
Emerging markets are also playing an increasingly important role in the global PET blow molding machine market. These regions are experiencing rapid economic growth and a growing demand for plastic packaging, which has led to an increased adoption of PET blow molding machines. As a result, manufacturers in these markets are investing in research and development to produce machines that are tailored to the local market conditions.
Looking Ahead
With continuous technological innovations and a growing emphasis on environmental consciousness, the PET blow molding machine industry is on the cusp of a new era filled with both opportunities and challenges. The application of new technologies, such as artificial intelligence and 3D printing, holds great promise for further improving the efficiency and performance of PET blow molding machines. For example, artificial intelligence can be used to optimize the production process by predicting maintenance needs and adjusting production parameters in real - time.
The promotion of circular economies will also continue to be a major focus. As more companies and consumers embrace the concept of recycling and sustainable packaging, the demand for PET blow molding machines that can handle recycled materials will only increase. This will drive manufacturers to develop more advanced and efficient recycling - compatible machines.
In addition, the increasing consumer demand for sustainable packaging will remain a key driver of innovation in the industry. PET blow molding machine manufacturers will need to continue to invest in research and development to create machines that can produce even more sustainable and high - quality plastic bottles. This may involve the development of new materials, more efficient production processes, and innovative designs that meet the evolving needs of the market.
In conclusion, the future of PET blow molding machines will be characterized by a strong emphasis on green initiatives and product innovation. By prioritizing these aspects, the industry will be able to create more possibilities and dynamism within the plastic packaging sector, ultimately contributing to a more sustainable and prosperous future.