Discover the Future of Plastic Manufacturing with Dawson Blow Molding Solutions
Explore premium equipment and methods for blow molding that define efficiency, precision, and versatility in the plastic manufacturing industry.
Fully Automatic Blow Molding Solution for Plastic Manufacturing
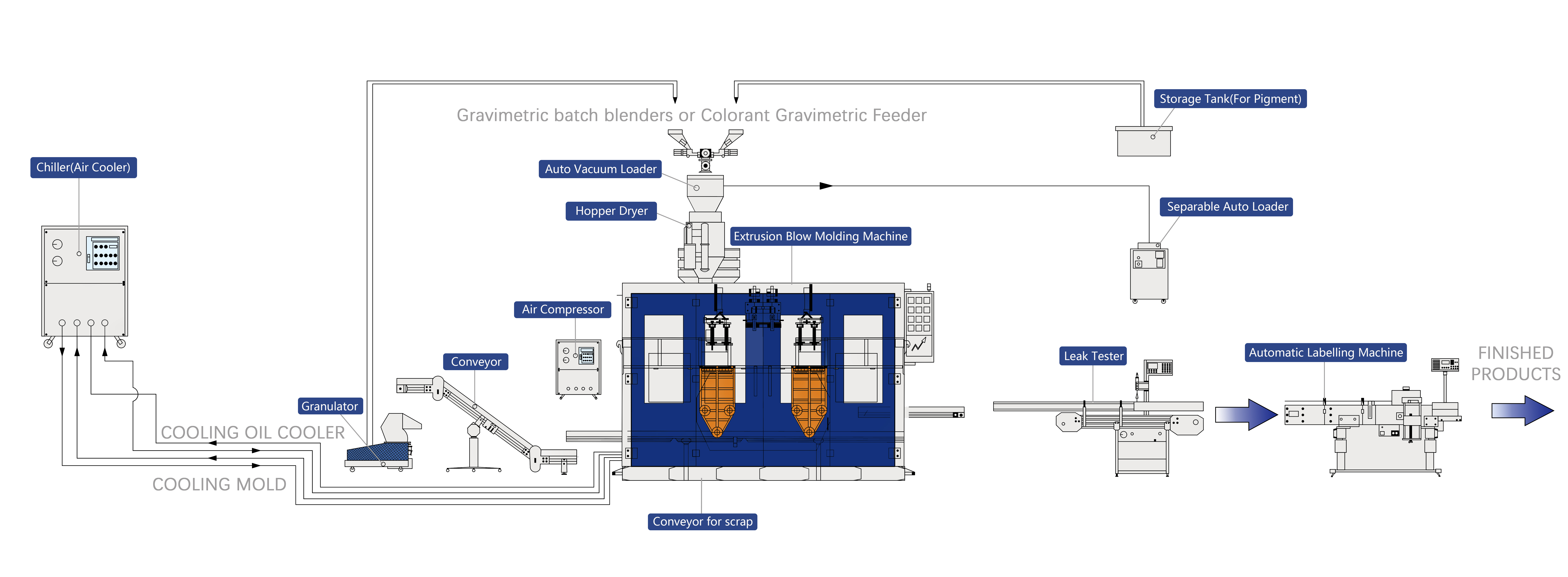
High-performance Blow Molding Equipment and Blowing Mould
Our blow molding solutions include high-performance automatic machine equipment , precision blowing moulds and essential auxiliary equipment. Designed for efficiency and versatility, our systems ensure superior production quality across various industries.
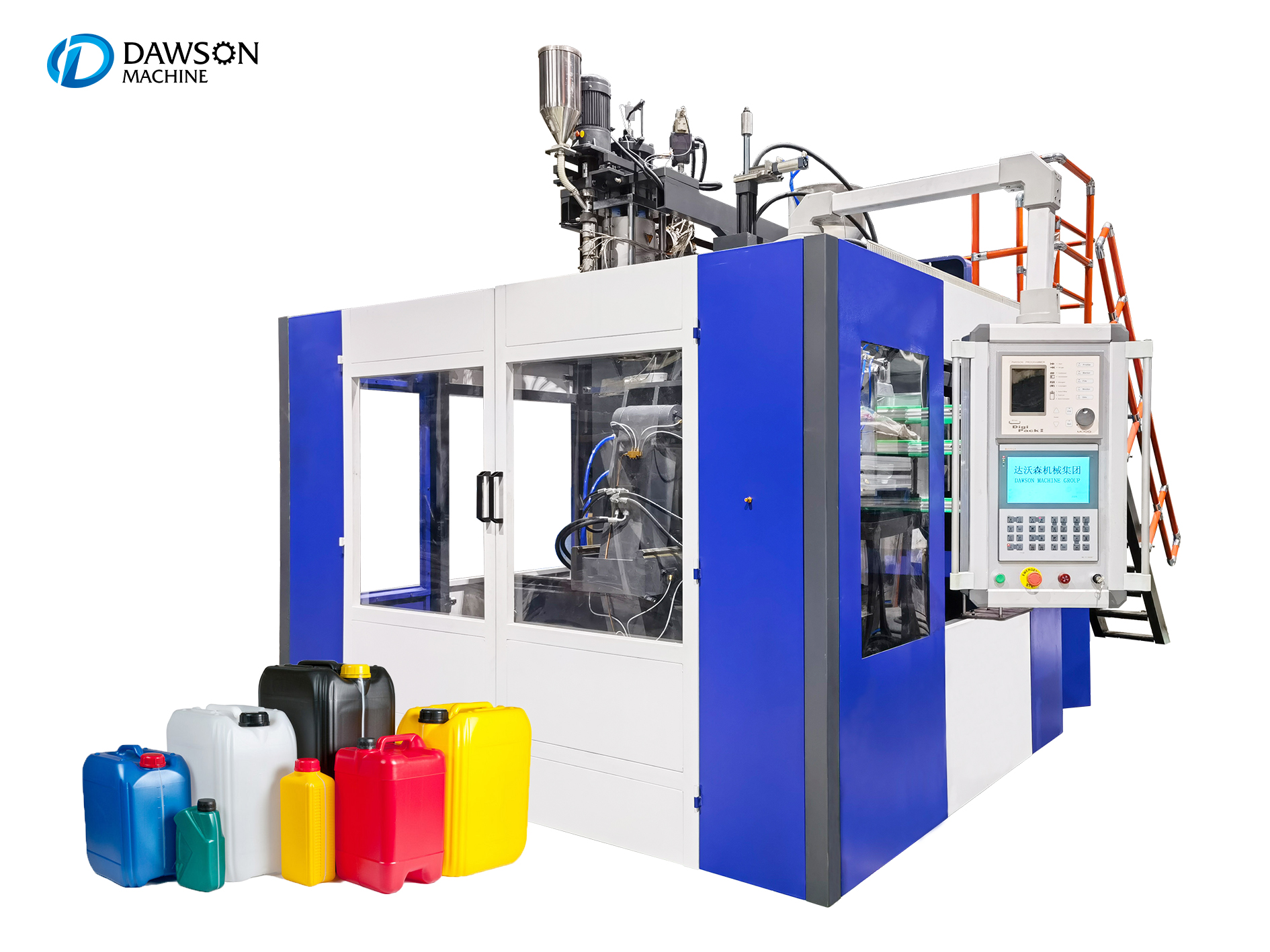
Blow Molding Equipment
This extrusion blow molding machine, is suitable for producing 10L to 30L plastic jerry can for lubricant oil, daily chemical, edible oil, etc.
Production capacity:50-60pcs/hour for 1.0kg 20L jerry can
Continuous type die head
Toggle type clamping system
Servo hydraulic system
With auto deflashing function
Parison controlling system(MOOG, Xunjie or Wisetech according to your requirement)
Liquid level line system(optional)
Mould can be manual deflashing or auto deflashing
Blow Molding Mold
Mould material P20# / S136H / Aluminium 7075#
Mould neck, bottom and middle parts are separable.
Separate cooling system for mould neck, mould body and bottom.
Min 2 million mould life.
Optional to make interchangable parts of 20L/25L/30L
Mould can be made manual deflashing or auto deflashing.
Optional to add inserts to make customer LOGOs or UN LOGOs
Other jerry cans designs optional for customer to choose
Jerry can cap mould can also be provided.
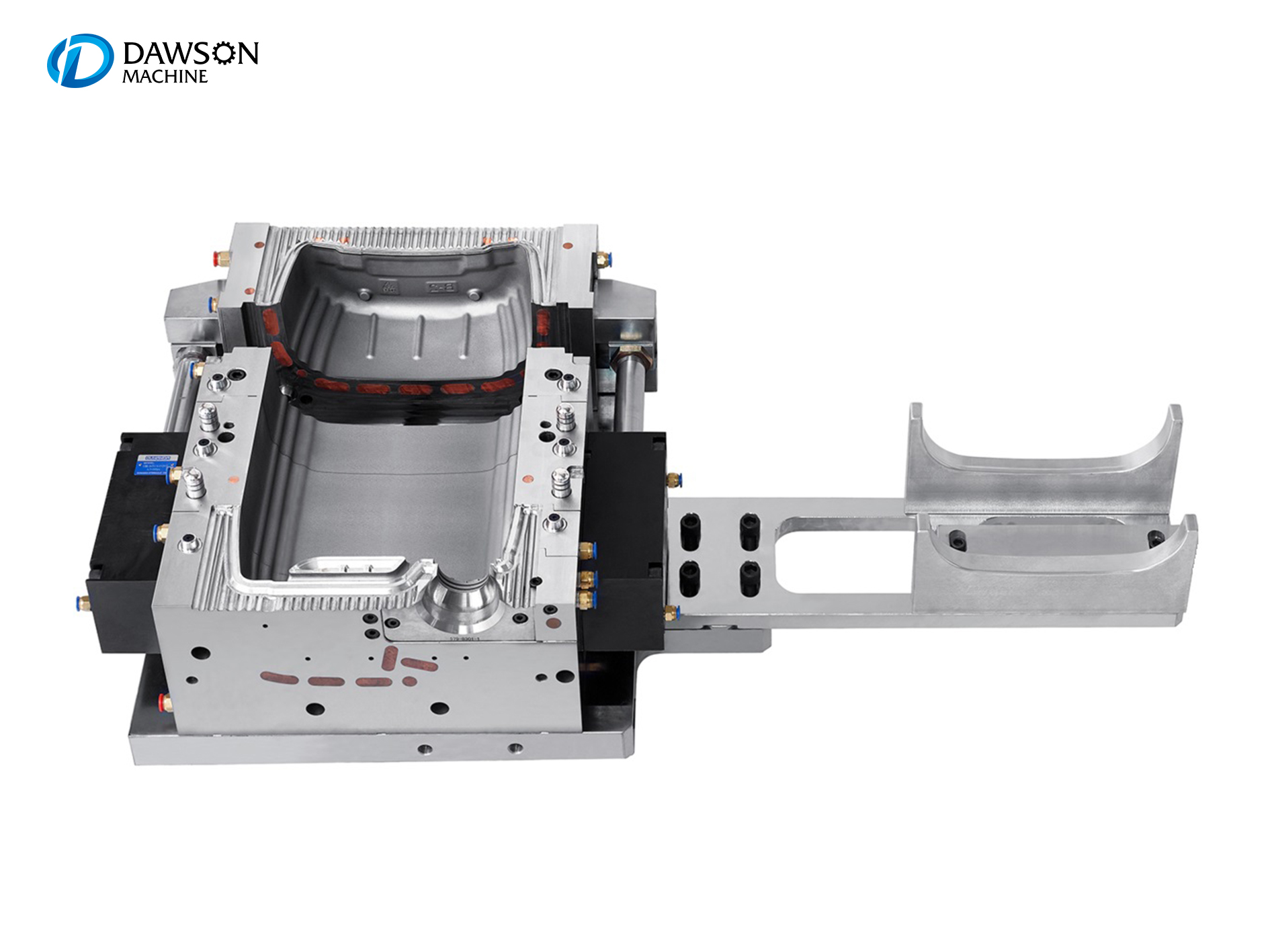
Related Products for Blow Molding Machine
Blow Molding in Plastics Processing
Blow molding is a cutting-edge procedure that's utilized in the plastic industry to create hollow objects by inflating a hot, porous thermoplastic tube into a mold and then changing the shape. This method combines efficiency with flexibility, which is ideal for creating a variety of products.
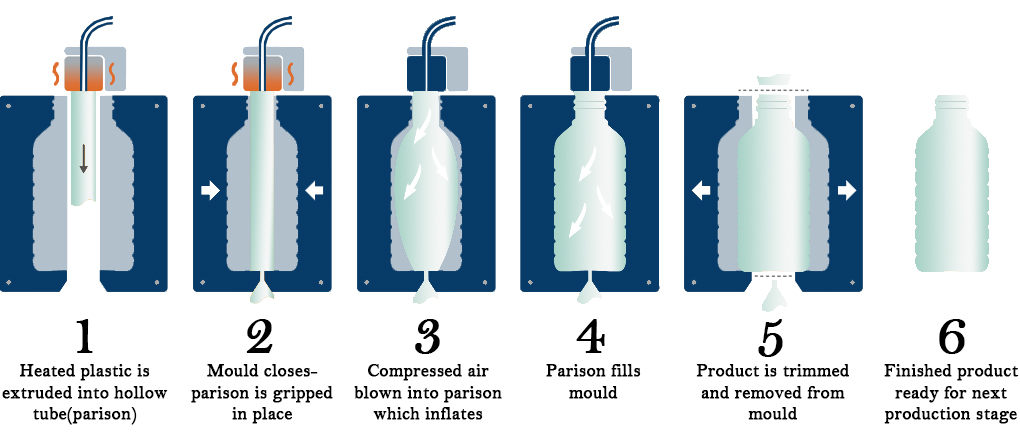
Blow Molding Application:From Pharmaceuticals to Automotive
Versatile Bottle Sizing for Every Need
Whether you're attempting to produce small bottles for cosmetics or large containers for industrial use, our versatile equipment supports a variety of sizes. Precision controls ensure that the thickness of the products is consistent and of high quality.
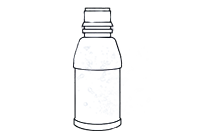
100ml - 1L

100ml - 1L
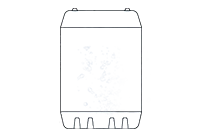
10L - 30L
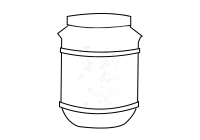
100ml - 1L
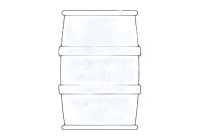
over 100L
Selecting the Perfect Material for Optimal Performance
We specialize in dealing with a variety of materials including HDPE, LDPE, PP, PVC, and PETG. Our expertise ensures that the material selection for each project is effective, while maintaining a cost of effectiveness with a performance goal.
In the process of blow molding, selecting the right material is crucial. Here are some primary materials with their advantages and application scenarios to help you achieve optimal performance:
Material | Advantages | Application Scenarios |
HDPE (High-Density Polyethylene) | High strength-to-density ratio; Impact resistant; Weather resistant; Recyclable; Low moisture absorption; Resists mold, mildew, rotting | Containers for milk, detergents, and bleaches; Fuel tanks for vehicles |
LDPE (Low-Density Polyethylene) | Excellent flexibility; Ease of processing; High ductility; Low-temperature resistance | Squeeze bottles; Food storage containers; Flexible lids and snap-on lids |
PP (Polypropylene) | Strong chemical resistance; Elasticity and toughness; Fatigue resistance | Automotive parts like bumpers and dashboards; Food containers due to its high melting point |
PVC (Polyvinyl Chloride) | Durable under stress and compression; Flame retardant properties; Good clarity and brightness | Non-food item packaging such as shampoo bottles or cleaning agents' containers |
PETG (Polyethylene Terephthalate Glycol-modified) | Excellent clarity and gloss for premium aesthetics; High impact resistance making it shatter-proof; Easy to form and customize | Medical device packaging requiring clear visibility or retail packaging showcasing product appeal |