DAWSON MACHINERY & MOULD GROUP
Extrusion Blow Molding Machine ABLD120
Ⅰ. Versatile Container Production Capabilities
Our extrusion blow molding machine has been meticulously engineered to meet the diverse demands of the plastic container manufacturing industry. It truly shines when it comes to its suitability for creating a wide array of plastic products. Notably, it is highly adept at making plastic drums, barrels, and large containers, with its size range extending up to a maximum capacity of 250 liters. This broad spectrum of possible volumes caters to an extensive variety of applications.
In the market, we commonly observe that our customers predominantly utilize this machine to produce specific and popular sizes. The 200L, 210L, 215L, and 235L double L-ring plastic drums are among the most frequently manufactured items. These sizes have become industry standards due to their optimal balance between storage capacity and practical handling. For instance, the 200L drum is widely favored in the chemical and petroleum sectors for transporting and storing bulk liquids. Its double L-ring design provides enhanced structural integrity, ensuring safe containment during transit. The 210L and 215L variants offer slightly more volume, making them suitable for applications where a bit of extra capacity is required without sacrificing too much on portability. Meanwhile, the 235L drum is often chosen for industries dealing with heavier substances that need to be stored in larger quantities but still within a manageable size for loading and unloading operations.
Ⅱ. Material Compatibility and Quality Assurance
To achieve the highest quality in the produced plastic containers, our machine is designed with a deep understanding of various plastic materials. It demonstrates excellent compatibility with the polymers commonly used in drum manufacturing, such as high-density polyethylene (HDPE). This material is renowned for its durability, chemical resistance, and ability to withstand harsh environmental conditions. When processed by our extrusion blow molding machine, HDPE is transformed into robust and reliable containers.
The manufacturing process is carefully controlled to ensure consistent wall thickness and overall structural integrity. Our advanced temperature control systems and precise extrusion mechanisms work in tandem to prevent issues like uneven melting or weak spots in the final product. This attention to detail means that each plastic drum, regardless of its size, meets stringent quality standards. Whether it's destined to hold corrosive chemicals, food-grade substances, or industrial lubricants, our customers can have full confidence in the reliability and safety of the containers produced.
Ⅲ. Innovative Die Head and Molding Technologies
At the heart of our machine's exceptional performance lies the innovative die head and molding technologies incorporated. The specially designed die head allows for precise shaping and sizing of the plastic drums. It features adjustable parameters that can be fine-tuned according to the specific requirements of each production run. For example, when switching between the production of different-sized drums like the 200L and 235L, the die head can be quickly and accurately reconfigured to ensure seamless transitions.
Our molding process also incorporates state-of-the-art techniques to enhance the overall quality and appearance of the drums. This includes features such as smooth surface finish control, which is crucial for both aesthetic appeal and functionality. A smooth surface not only gives the drums a professional look but also reduces the risk of dirt and debris accumulation, making them easier to clean and maintain. Additionally, the molding process is optimized to minimize material waste, contributing to cost savings and environmental sustainability.
Ⅳ. Energy Efficiency and Production Speed
In today's competitive manufacturing landscape, energy efficiency and high production speed are key factors for success. Our extrusion blow molding machine addresses these aspects admirably. It is equipped with energy-saving components and intelligent power management systems. During the extrusion and blowing processes, power consumption is carefully monitored and optimized. For instance, the heating elements are designed to heat up quickly and maintain a stable temperature with minimal energy wastage, reducing overall electricity bills.
When it comes to production speed, our machine can achieve remarkable throughput. Thanks to its efficient design and automated features, it can produce a significant number of plastic drums per hour. This rapid production rate allows manufacturers to fulfill large orders promptly, meeting tight deadlines and gaining a competitive edge in the market. Even when producing the more complex double L-ring drums, the machine doesn't sacrifice speed for quality, ensuring a seamless production flow.
Ⅴ. User-Friendly Operation and Global Support
User experience and operational simplicity are top priorities in the design of our blow molding machine. As mentioned, the whole machine is equipped with a bilingual operation panel. This feature breaks down language barriers and enables operators from different regions and language backgrounds to easily understand and control the machine. Whether it's in an international manufacturing facility with a multicultural workforce or a company expanding globally, this user-friendly interface ensures smooth operation.
In addition to the intuitive panel, the machine incorporates automatic configurations sourced from world famous brands. These components not only enhance the machine's performance but also provide reliable and easy-to-maintain systems. Our global support network further complements this. We offer comprehensive after-sales service, including technical assistance, spare part supply, and training programs. This means that regardless of where our customers are located, they can rely on us to keep their production lines running smoothly and efficiently, maximizing the return on their investment in our equipment.
Name |
Units | DSBD120 |
Max.product volume | L | 250L |
Screw diameter | MM | 120 |
Screw drive power | KW | 90 |
Output of HDPE | KG/H | 320 |
Oil pump drive power | KW | 37 |
Clamping force | KN | 820 |
Max.size of mold | MM | 900× 2000 |
Template size | MM | 1400×1800 |
Mold stroke | MM | 800-1800 |
Size of machine | L×W×H | 8.6×3.8×35.8 |
Weight of machine | TON | 38 |
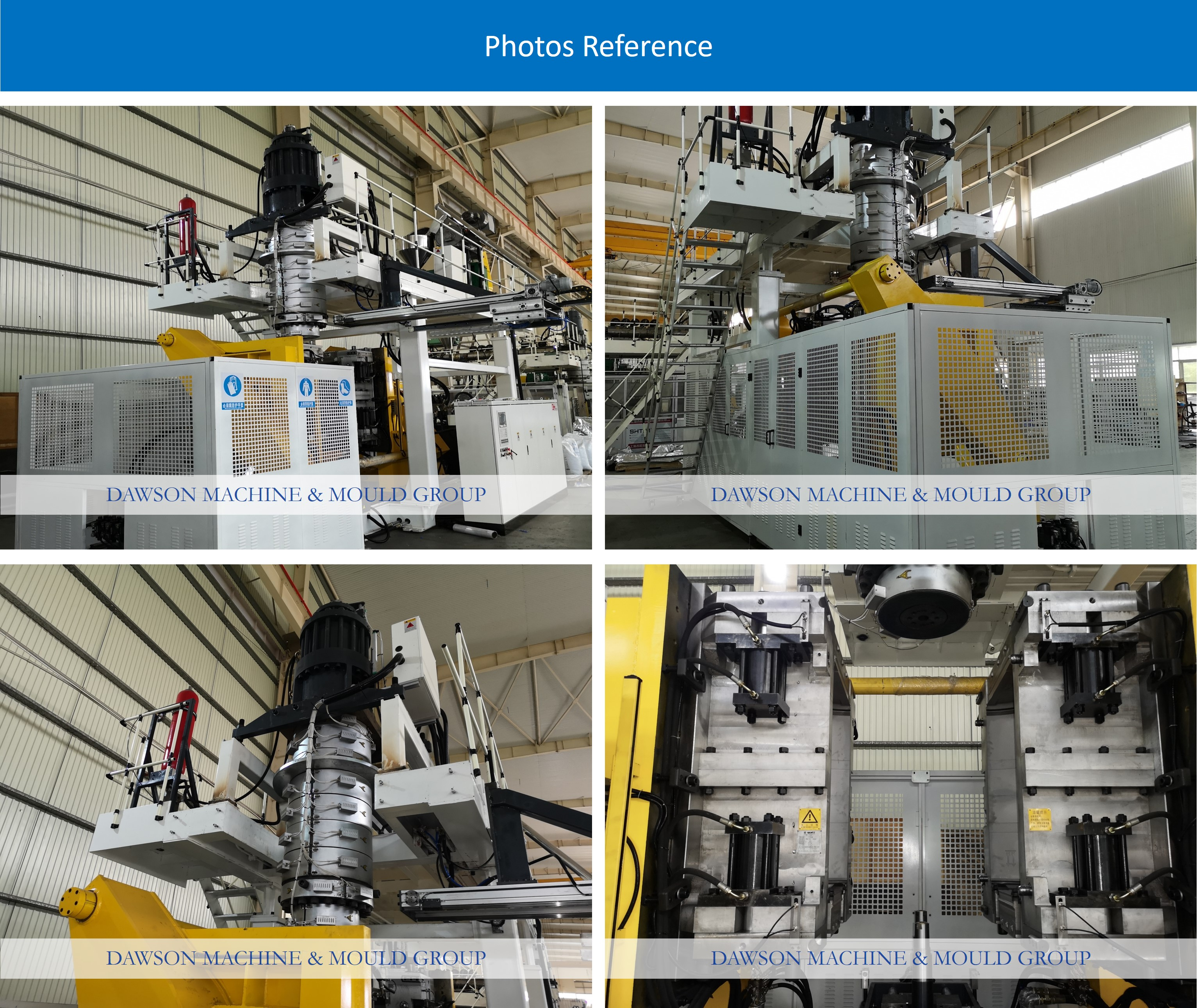
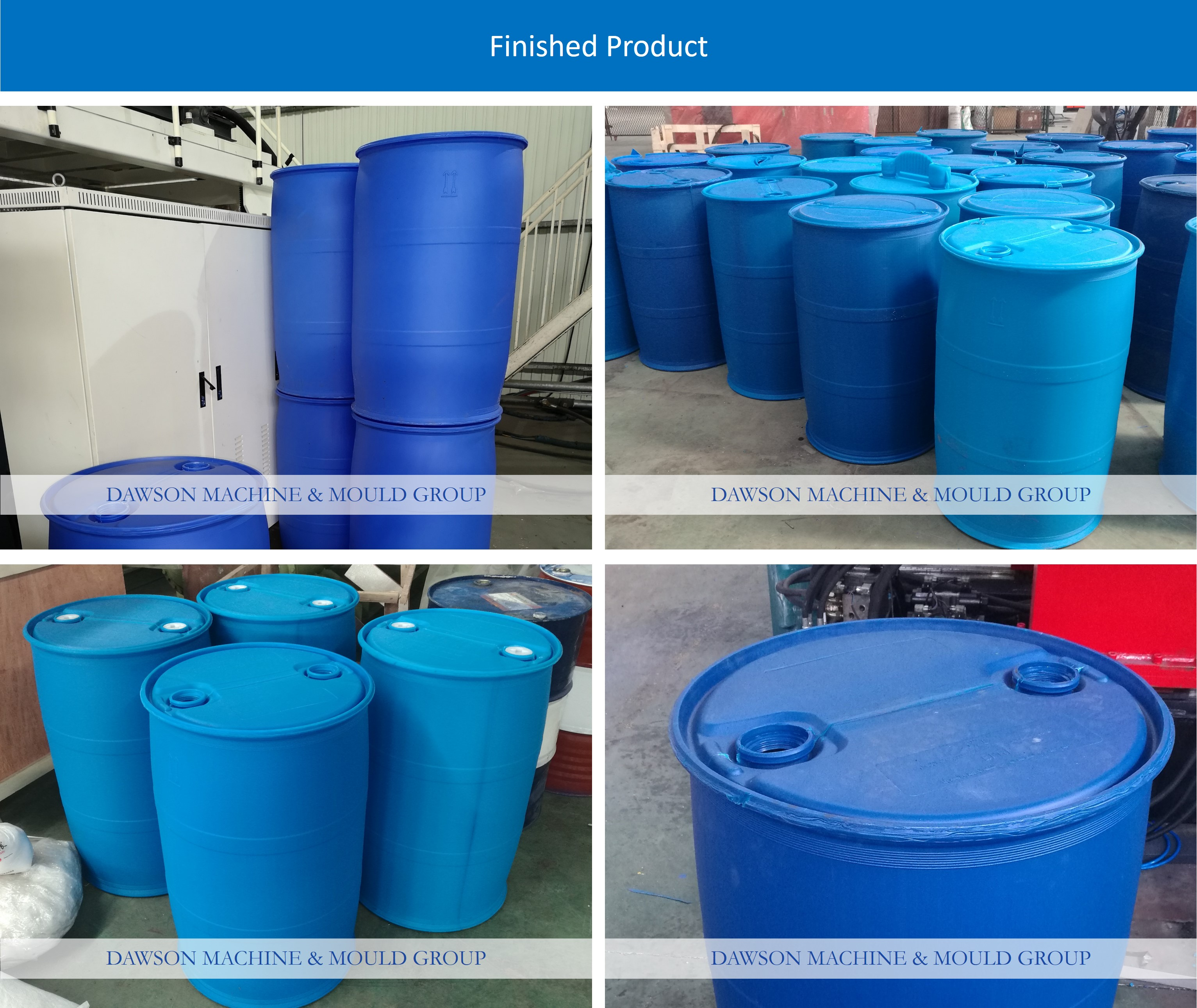