Automatic Double Station Double Head Extrusion Blow Molding Machines For hanging bottle pp
DESCRIPTION
Our state-of-the-art Automatic Double Station Double Head Extrusion Blow Molding Machines, crafted by Dawson, are the ultimate solution for crafting high-quality hanging bottles made from PP (polypropylene). Engineered with precision and innovation, these machines offer a seamless production process, exceptional customization capabilities, and top-notch safety features.
Extrusion Blow Molding Process
The extrusion blow molding process employed by our machines is a marvel of modern engineering, a carefully orchestrated sequence that guarantees the creation of flawless hanging bottles. It commences with the plastic resin, typically in pellet form, being fed into the machine's hopper. From there, the resin descends into the extruder, a robust component equipped with a specialized screw. As the screw rotates, it not only conveys the resin forward but also subjects it to intense mechanical shearing and heat, gradually transforming the solid pellets into a molten, viscous mass.
Once the plastic resin reaches the desired molten state, it is extruded through a precisely designed die, giving birth to the parison - the hollow tube that will form the basis of the hanging bottle. The dimensions of the parison, including its diameter, length, and wall thickness, can be meticulously adjusted. For instance, by modifying the speed of the extruder screw, the temperature profile within the extruder barrel, and the geometry of the die, we can fine-tune the parison to meet the exact requirements of different hanging bottle designs.
Subsequently, the freshly formed parison is rapidly transferred to the mold. Our double-station, double-head configuration allows for two parisons to be processed simultaneously, effectively doubling the production capacity. The mold, which is custom-machined to replicate the intricate details of the hanging bottle, closes around the parison, sealing it at both ends. Compressed air is then forcefully introduced into the parison through an air inlet. The pressure of the air causes the molten plastic to expand and conform precisely to the contours of the mold cavity. This inflation process is carefully regulated to ensure uniform wall thickness and consistent product quality.
After the plastic has fully expanded and taken on the shape of the mold, the cooling phase begins. Our machines are equipped with advanced cooling systems that utilize a combination of water-cooled channels within the mold and external air-blowing mechanisms. This dual cooling approach rapidly dissipates the heat from the plastic, causing it to solidify and acquire the desired strength and rigidity. Once the cooling process is complete, the mold opens, and the finished hanging bottle is gently ejected using a pneumatic ejection system, ready for further inspection, packaging, and distribution.
Machine Customization
At Dawson, we understand that every production facility has unique requirements, and that's why we offer extensive machine customization options. Our team of experienced engineers works closely with clients to design and build machines that are tailored to their specific needs.
Dimensions and Space Adaptation : One of the key aspects of customization is adapting the machine's dimensions to fit the available production space. Whether you have a small, compact factory floor or a large industrial facility, we can modify the length, width, and height of the machine to ensure a seamless integration into your production line. For example, if your factory has limited ceiling height, we can design a low-profile version of the machine without compromising on its performance or functionality.
Feature Additions : We also offer a wide range of optional features that can enhance the capabilities of the machine. These include advanced temperature control systems for more precise resin melting, high-speed extrusion heads for increased production rates, and intelligent parison programming systems that can automatically adjust the parison dimensions based on the bottle design. Additionally, we can add features such as automatic label applicators, inline quality inspection systems, and integrated weighing stations to streamline the production process and improve product quality.
Auxiliary Equipment Integration : To further optimize your production process, we can integrate various auxiliary equipment into the machine. Robotic systems, for instance, can be incorporated for handling and packaging the finished hanging bottles. These robots can be programmed to pick up the bottles from the ejection area, place them in trays or boxes, and even stack the boxes for easy transportation. Other auxiliary equipment that can be integrated includes conveyor systems for seamless material handling, drying units to ensure the resin is at the optimal moisture level, and granulators for recycling scrap plastic.
Safety Features
At Dawson, safety is our top priority. We have incorporated a comprehensive range of safety features into our Automatic Double Station Double Head Extrusion Blow Molding Machines to create a secure working environment for operators.
Emergency Stop Buttons : Strategically placed throughout the machine, emergency stop buttons are easily accessible to operators. In the event of an emergency, a simple press of the button immediately halts all machine operations, bringing the moving parts to a safe stop. This ensures that any potential hazards can be quickly addressed, minimizing the risk of injury to operators.
Safety Interlocks : Our machines are equipped with safety interlocks that prevent the machine from operating when access doors or protective guards are open. These interlocks are designed to detect any unauthorized entry into potentially dangerous areas of the machine. For example, if the mold access door is opened during the production process, the machine will automatically stop, and the power will be cut off to the relevant components. This not only protects the operators from coming into contact with moving parts but also safeguards the machine from damage.
Protective Guards : To shield operators from direct contact with moving parts, hot surfaces, and other potential hazards, our machines are fitted with robust protective guards. These guards are made from high-quality materials and are designed to withstand the rigors of daily use. They cover critical areas such as the extruder, the mold clamping mechanism, and the moving arms, providing a physical barrier between the operators and the machine's dangerous components.
In addition to these primary safety features, our machines also come with comprehensive safety manuals and operator training programs provided by Dawson. The safety manuals provide detailed instructions on how to operate the machine safely, as well as guidelines for maintenance and troubleshooting. Our operator training programs ensure that all personnel who work with the machine are fully trained in safety procedures and are aware of the potential hazards associated with the equipment.
When considering the purchase of an extrusion blow molding machine for hanging bottle production with PP, it is essential to conduct thorough research, review detailed technical specifications, and consult with reputable manufacturers. At Dawson, we are committed to providing our clients with the highest quality machines, exceptional customization options, and unwavering safety standards. Contact us today to learn more about how our Automatic Double Station Double Head Extrusion Blow Molding Machines can transform your production process.
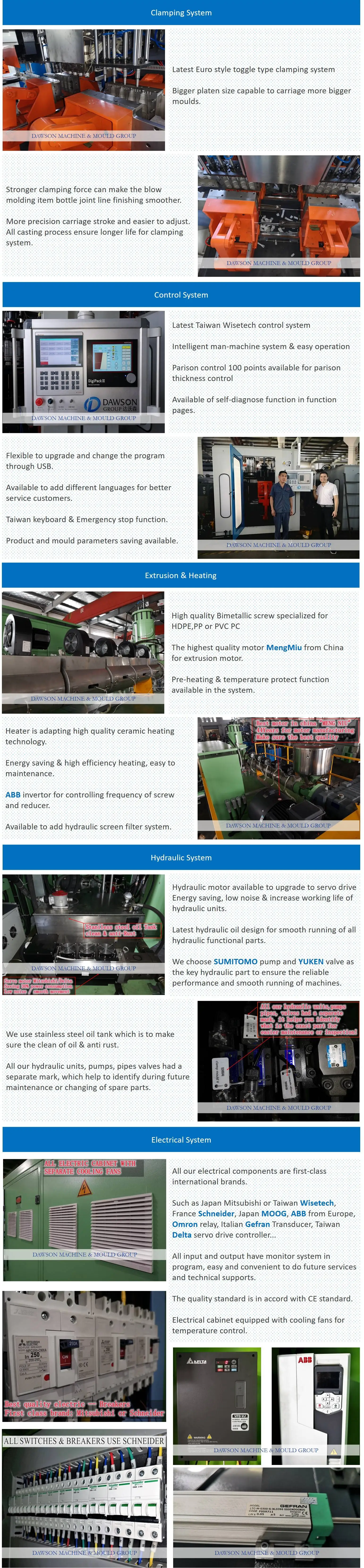
Technical Parameter
Application